Our process.
Take advantage of amazing design flexibility, a quick turnaround, and quality assurance.
From project consultation to shipment, our experienced team and our state-of-the-art machining and powder application ensure a product that exceeds your expectations and can be used in many applications.
Our Wood Powder Coating Process
Play Video
Customer Consultation
Preparation & Coating
Quality Control
Assembly & Warehousing
Customer Consultation
We know the details can be overwhelming, so we’re here to help navigate the decisions to reach the appropriate solution for your application:
- t.fusion™ texture and gloss requirements
- Color effects and matching
- MDF board specifications
- Performance characteristics
- Project scheduling and lead times
- Assembly, warehousing, and shipping
Preparation & Coating
Quality products require a quality process. Our proprietary part preparation process and high-tech equipment are integral to ensuring we deliver the best results.
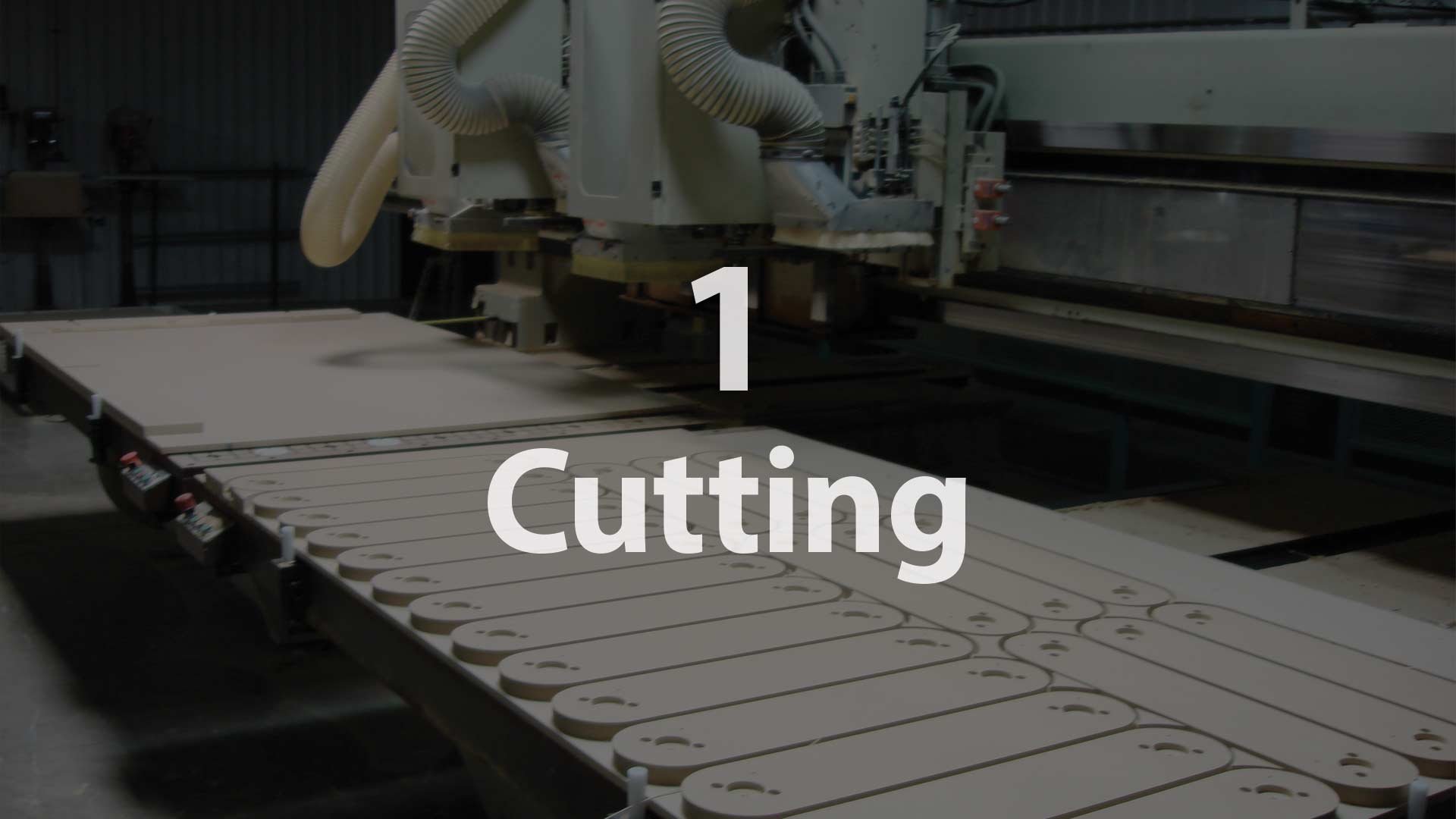
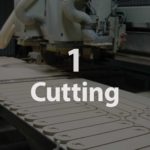
The timing between MDF cutting and coating is critical for controlling moisture content. To minimize that time, we’ve invested heavily in in-house CNC machinery and skilled staff.
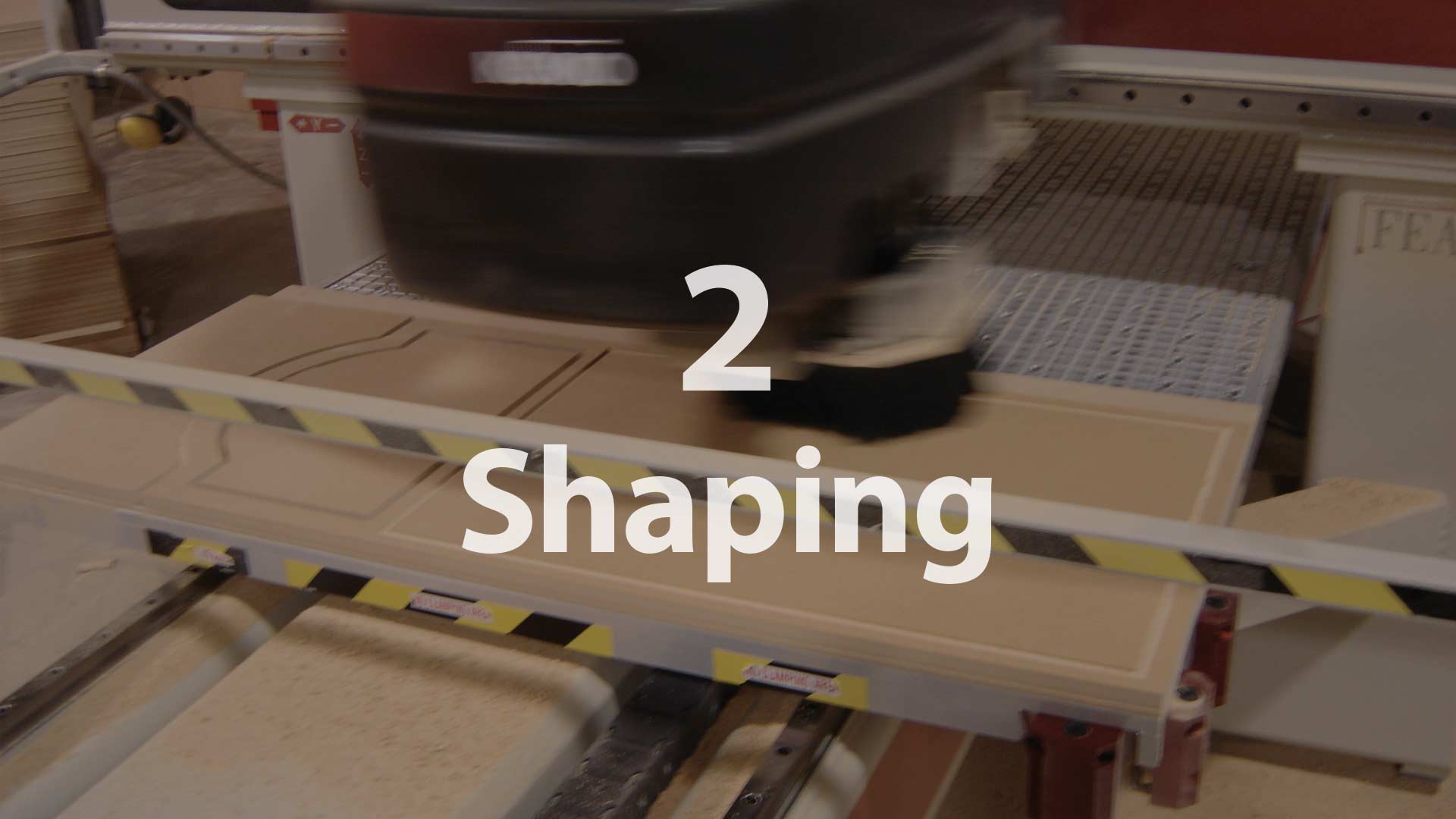
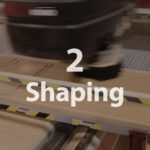
Precise contours, profiles, and cutouts are possible with our CNC-controlled routers and large tooling library.
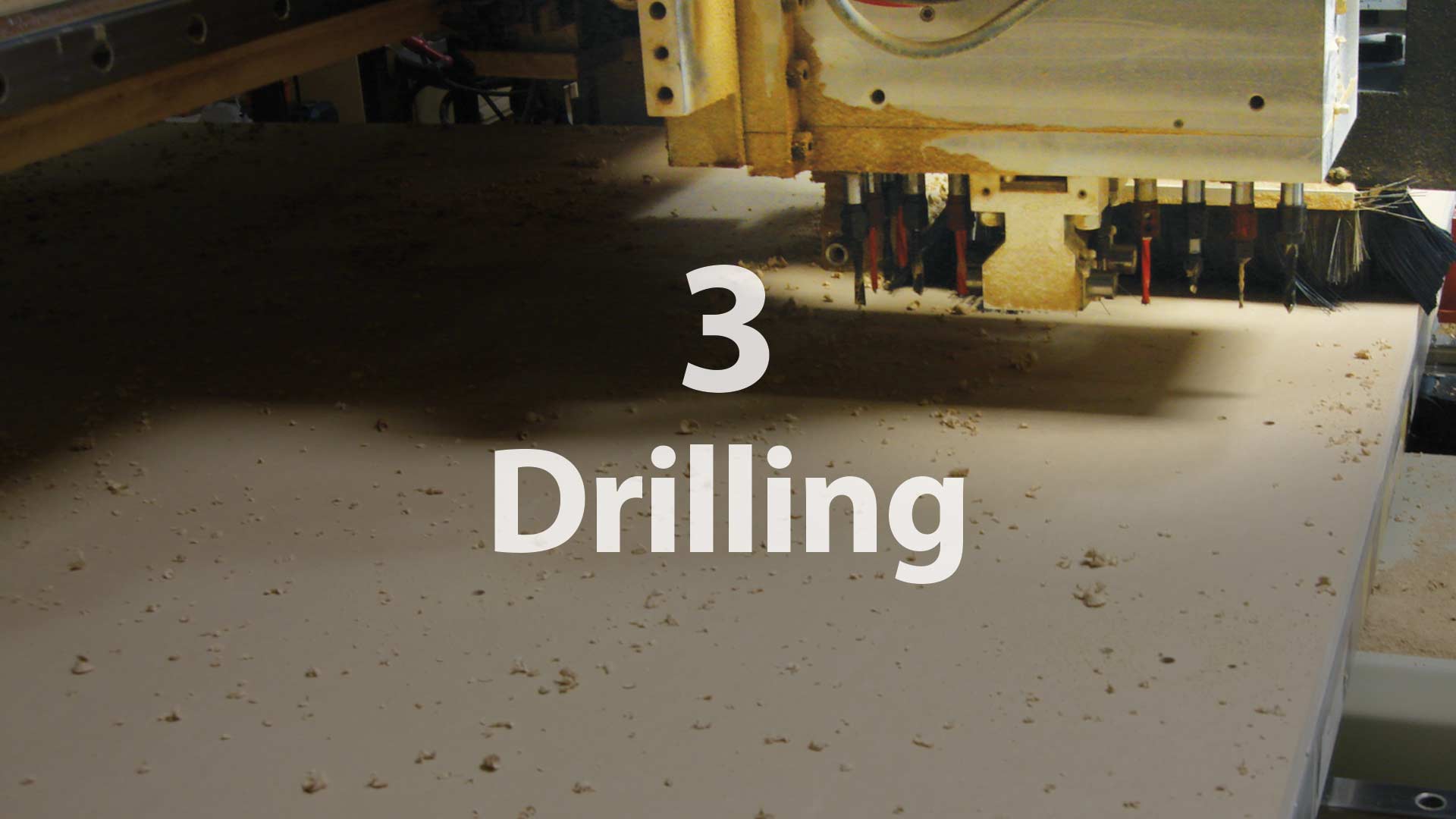
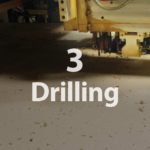
Complex drilling requirements can be fulfilled either on the router or by utilizing one of our drilling machines.
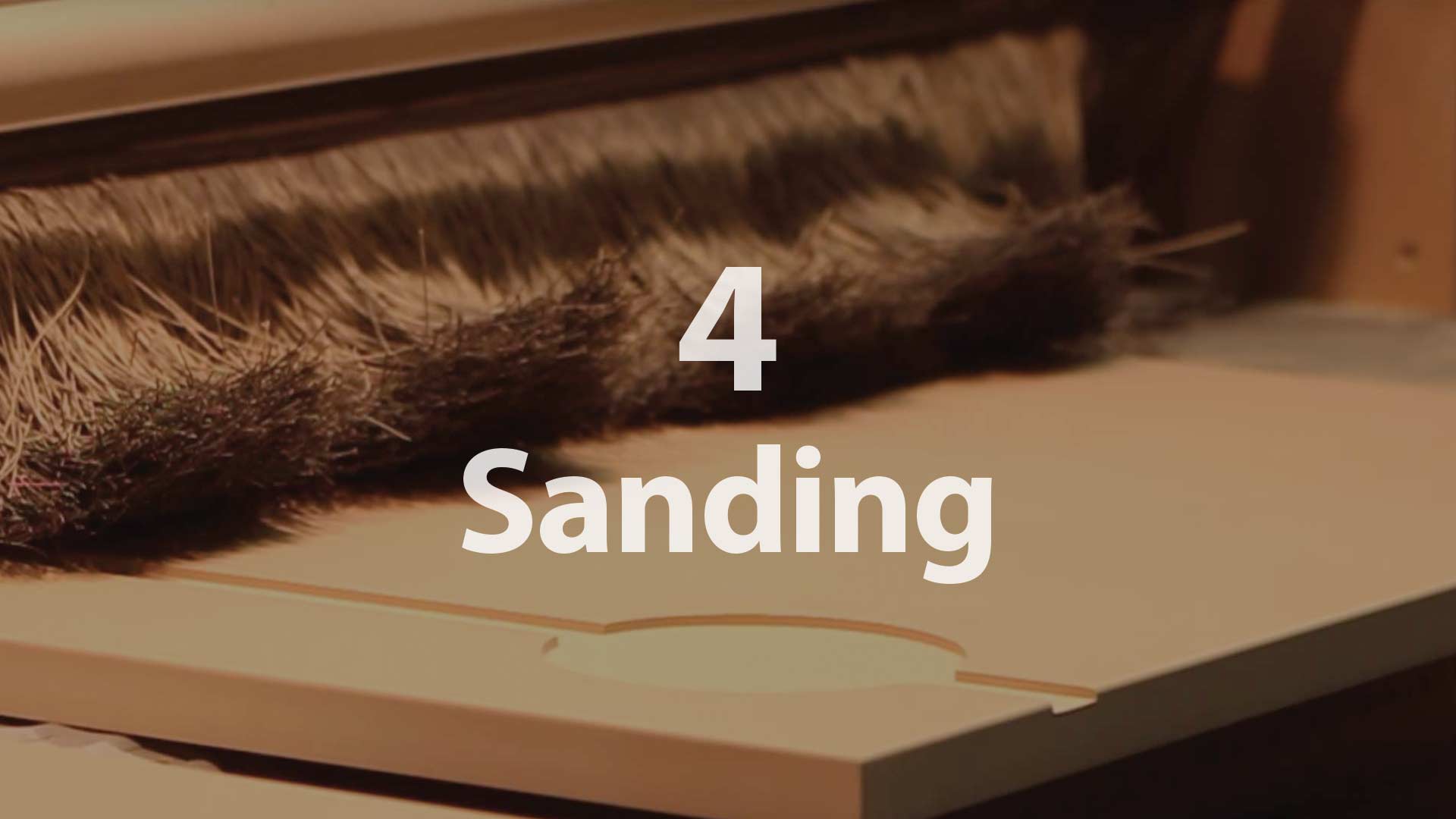
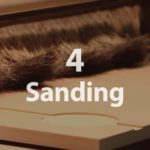
Our automated conveyor system has multiple sanders, and we sand particularly complex shapes by hand.
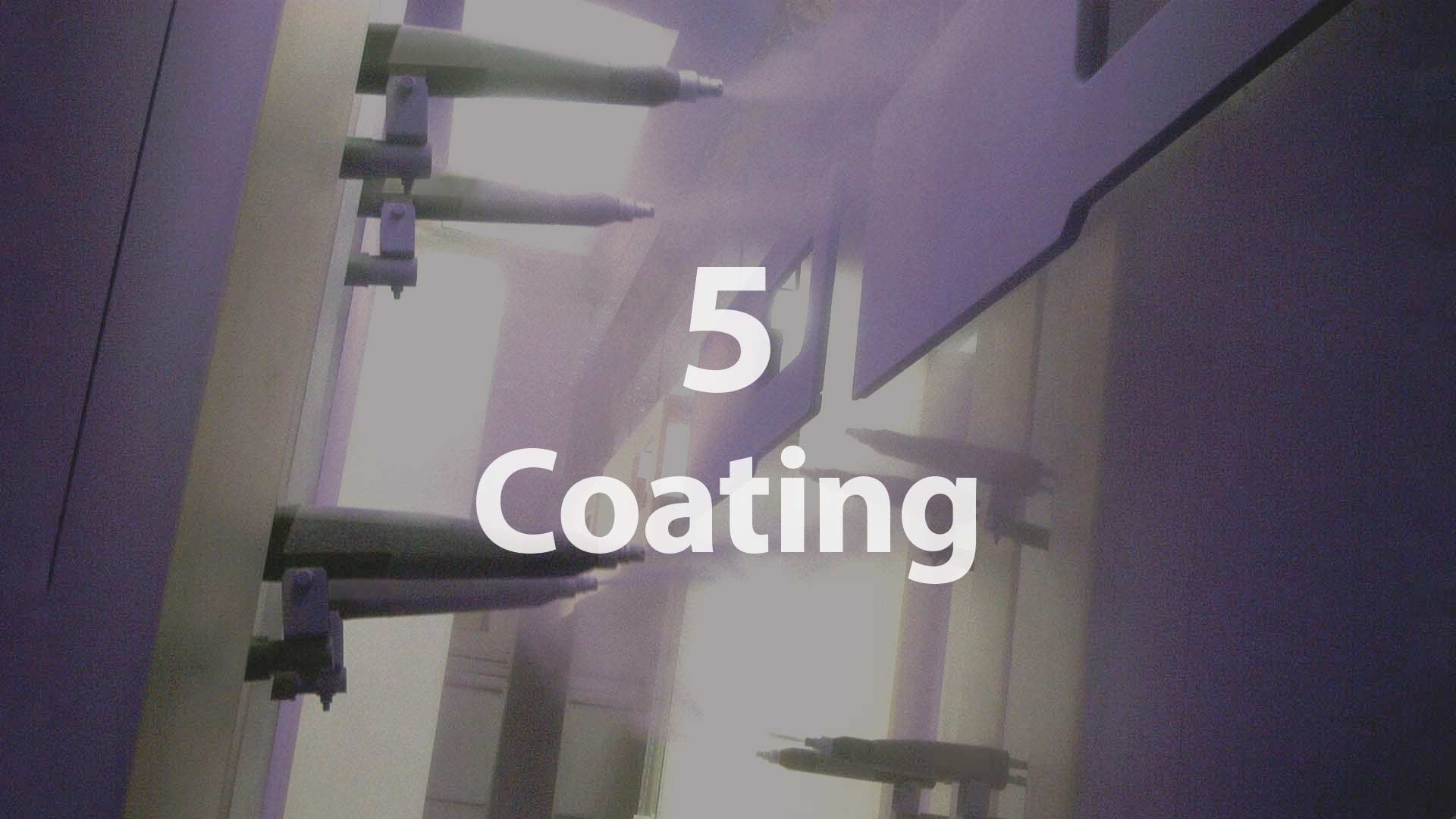
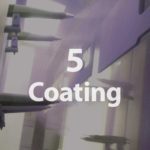
The final step is coating with powder, which involves a process of pre-heating the wood, spraying the powder onto the wood, getting the powder to the right temperature for it to cure, and finally cooling it again. Our in-house experts make sure all of these steps are performed to the highest quality standards.
Technology
Our ongoing R&D keeps us at the forefront of technological innovations to provide the most economical and durable finishes with a quick turnaround.
- Multiple CNC nesting routers, drilling machines, and sanders
- State-of-the-art wood powder coating system
- Proprietary part preparation, curing, and finish hardness processes
- Automated conveyor with brush sanding system
Quality Control
Quality is baked into everything we do. We meticulously perform a series of quality control tests and procedures to ensure you receive the highest quality product possible.
- Daily machine calibration
- Examination of all incoming materials
- Just-in-time MDF purchasing to maintain a fresh, consistent supply
- Verification of each incoming powder batch against a master
- Dedicated lighting at each station to detect defects throughout our manufacturing process
- Custom packaging to reduce the risk of damage during shipping
- Inspection of all parts prior to assembly or shipping to ensure durability and proper component fit
Quality Tests
- Mil thickness
- Fatty edges
- Cure
- Adhesion
- Color match
- Color uniformity
- Coverage uniformity
- Gloss reading
Key Performance Indicators
- Defective parts per million (DPPM), measured per operation
- Customer complaints per million opportunities (CCPMO)
- First pass yield (FPY)
- Complete and on-time delivery (COT)
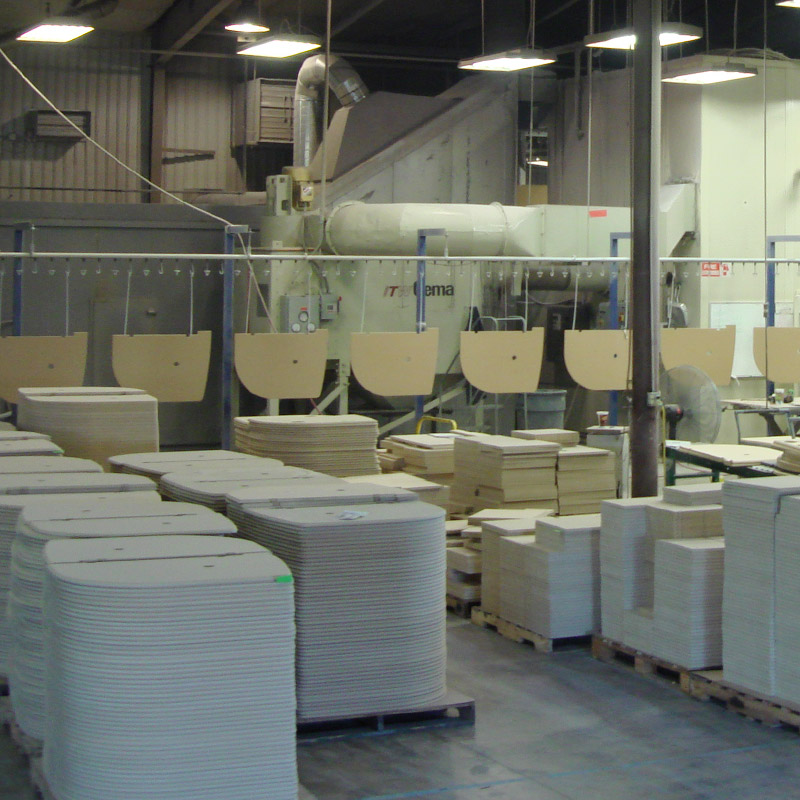
Assembly & Warehousing
We can ship fully or partially assembled units and project manage any outsourced component parts, such as plastic, metal, printed surface graphics, and packaging.
Need to keep your parts at our warehouses? We can do that too.
Want to learn more?
Need it done quickly?
We collaborate closely with our powder suppliers to get powder when we need it, and we use the right technology to accommodate quick turn around times.