Featured in Powder Coating Magazine. Written by: Craig Martin, President BTD Wood Powder Coating
The quality of a powder coated finish varies across manufacturers and can be manifested visually or beneath the surface. A quality powder coated MDF finish is beautiful, durable, and consistent. The good news for end users is that the quality traits can easily be identified through visual examination, testing, or simply by asking the right questions. This installment of the column is meant to describe a quality powder coated wood finish, to help prospective buyers identify the differences, and to explain why these quality differences matter.
Consistency
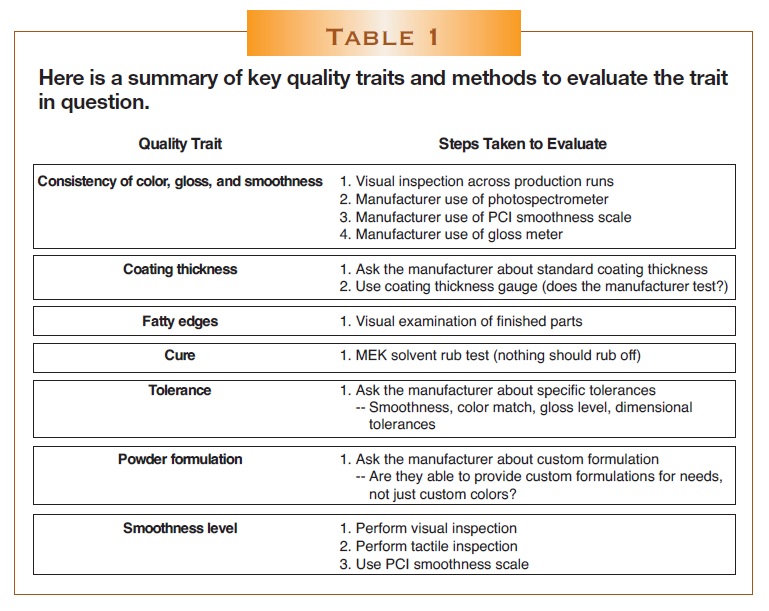
Mil Thickness
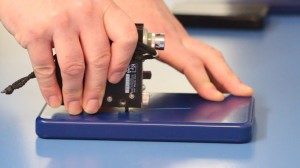
Fatty Edges
Cure
A quality powder coated MDF finish must be cured properly before shipment. Proper cure is important because it ensures the finish is completely bonded to the substrate and has all of the expected performance characteristics. An uncured finish might look good but is less durable. A standard MEK (methyl ethyl ketone) solvent rub test will confirm cure quality, since a cured finish will not rub off during the test. A side benefit of this test is that it will also identify whether liquid paint has been used to touch up any flaws. Liquid paint rubs off readily in the MEK rub test, while a good powder coated finish will stand up to the solvent.
Tolerance
As mentioned above, a quality wood powder coater will be able to produce a consistently high quality product. When working with company representatives, confirm mutual expectations for finish and machining tolerance. Robust process controls and quality inspections maintain tolerance ranges that are acceptable to both parties. A quality wood powder coater will be able to conform to specific PCI smoothness, CIELAB/ASTM color match guidelines, gloss ranges, and machining dimensional tolerances.
Powder Formulation
Powder formulation is a non-obvious variation that can be examined through research and testing. Knowledgeable wood powder coaters work with a variety of powder manufacturers and have established relationships to vary formulation based upon application and customer need. Powder can be formulated specifically for ultraviolet (UV) resistance, chemical resistance, or resistance to cracking. Performance characteristics of a coated part are directly affected by the powder formulation used; the best wood powder coaters will be able to understand the application (lab benches, drawer fronts, etc.) and recommend the most suitable formulation.